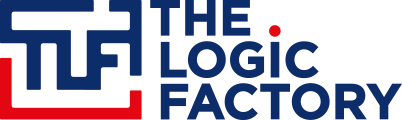
Equipment manufacturing is a juggling act involving the coordination of dozens if not hundreds of parts to ensure you have everything needed to assemble finished products on time to meet promised delivery dates. Any supplier shortfall, quality deviation, or skilled labor absence can send your best laid plans to the recycle bin.
The problem? ERP and spreadsheet-based planning tools don’t accurately reflect the reality of the shop floor. Lacking depth, they provide schedules that operators routinely ignore, choosing to work on what’s in front of them and available to work on. And who can blame them when it’s unclear which job in their department is both critical and feasible?
To solve this, you need planning and scheduling that is both robust and realistic:
Let’s take a look at some examples of common operational challenges and how you could solve them.
Quickly adapt to change
The situation on the ground changes every day. What-if scenario analysis enables you to explore all the possible solutions to untangle your planning knot and quickly find the best outcome.
Manage complexity
Create intelligent schedules that consider all the complexity of interrelated parts, sub-assemblies and their production timing.
Increase on-time delivery
Full visibility across the entire supply chain flow enables you to make commitments to customers, make promises you can keep, and realistic schedules the shop can adhere to.
Improve productivity
Optimize your plans to reduce setup time, maximize utilization of bottleneck resources and keep your operation running.
Commit with confidence
Create what-if scenarios to evaluate the impact of any changes to the plan before you commit, whether it’s overtime, a big new customer, or planned maintenance outage.
Perfect fit
Incorporate all the detailed rules and constraints of your business into planning logic, with solutions that perfectly align with and adapt to your unique business.