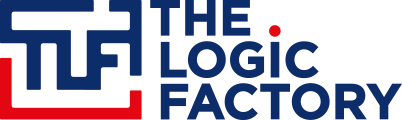
You’re on the precipice of a radical shift in how you operate. Forces beyond your control could have a damaging impact on your supply chain unless you take action. It’s time to redefine your operational resilience.
Metals and minerals organizations are grappling with unprecedented pressure, from market volatility and rising energy costs, to the need to minimize environmental impact.
Success hinges on making the best decisions across your value chain to drive efficient, future-ready operations. It’s more than just balancing operational and financial goals; environmental objectives are equally important. Sustainable optimization is the solution to successfully juggling this new trinity at all levels – planning, organization, and ecosystem.
Your planning teams can dynamically manage unpredictable blips in their plans when external or internal disruptions occur. With real-time data and the ability to model alternate scenarios, they are empowered to consistently deliver the most optimal plans.
Let’s explore some of your planning challenges.
Integrated decision making
Break down information silos that hinder visibility to achieve transparency on consumption, shipments, and inventory positions. Make business decisions confidently by locking your corporate KPIs into every planning decision.
Profit maximization
Identify opportunities to create value in your supply chain by calculating non-linear recoveries and valorizations, resulting in optimized planning in feed mix production, blending, and transportation. With optimal plans, you maximize your chances of boosting efficiency and profits.
End-to-end scenario optimization
Always be prepared by considering factors such as input costs/prices, transportation costs, market demands, and changes in production conditions. Assess the impact of ideas, investments, and decisions in the full end-to-end business context.
Optimized blending
With an optimizer, make SMART decisions on how to mix products in blending facilities, combine them in transportation, or place them in a smelter. Always know how long current blendable stock can support production, the risks, and the optimal way to move/consume products.
Complex constraint control
Optimize your business according to your KPIs while adhering to complex supply, production, and storage constraints. Instead of being reactive, your planners decide confidently when something fails or when constraints change – change in legislation, for example.
Sustainable optimization
Sustainable optimization will help you achieve your targets – operational, financial, and environmental. This is possible because all your KPIs, including sustainability targets, are embedded in the planning solution. So, all decisions are made with the impact on the organization and the environment in mind.
The energy transition hinges on the mining industry’s success. But how can producers effectively balance financial goals with environmental responsibility? Discover key trends and challenges reshaping the industry and learn how integrated supply chain planning is crucial for navigating the path to Net Zero.