Addressing Supply Chain Vulnerabilities in the Metals Industry
An Integrated Hybrid Solution for Your Metals Supply Chain Planning: Why You Need More Than An ERP System
A Support System to Lean On during the Oncoming Storm
The metals industry faces a period of falling profitability and supply chain insecurity. Manufacturers must strive for tighter efficiency in a world where revenues are under pressure and production must be done with less fossil fuel inputs. Raw material scarcity, interrupted transport routes, and higher prices add an additional layer of complexity. Whether producers are aware of it or not, a ‘perfect storm’ is brewing. In this context, supply chain planning becomes a key enabler.
The complexity and approach with supply chain planning in metals differs from the material and assembly-driven approach of industry in general. At the same time, the impact of good (or even improved) planning on costs, capital, and services is substantial. Some metals producers have gotten on board with implementing new technology to respond to the challenges and gain opportunities from better decision-making. However, the sector still has a lot of catching up to do.
Among producers who have implemented new technology, many are still using legacy systems today. They are not fit for a more complicated, unpredictable, and fast-changing business environment. Price, demand, raw materials, supply issues – there are just too many factors to consider now. Enterprise Resource Planning (ERP) systems have been employed to help streamline execution processes. They have contributed in that regard, but they don’t deliver when it comes to solving more complex metal planning puzzles. To compensate, spreadsheets and manual work are generally used to try and knit everything together.
Manufacturers have become aware of the potential headwinds they now face. They see that new levels of agility are needed and have begun to overhaul their processes and IT systems. ERP will still play a role in that endeavor, but companies must look further. The addition of an Advanced Planning System (APS) is essential to embed the necessary intelligence and optimization into the planning processes.
Why Is an ERP Not Enough?
While ERP has a key role to play, it’s not designed for detailed, optimization-driven supply chain planning. ERP systems look at things from a different angle, they grew up with a focus on finance and order processing. Transactional processes related to orders, purchasing, shipping, and finance remain their forte, but for planning and optimization, this material-driven approach typically falls short. A transaction-driven planning set-up will deliver a good plan for individual orders. However, it’s not possible to optimize across the order book or the entire company, especially when trying to include a range of relevant demands and constraints. ERP systems are materials-driven. Their planning logic works well in environments like assembly, where synchronizing material parts is the main challenge.
In the metals industry, challenges lie on the capacity side and in particular, ensuring planning meets specific rules as imposed by the metal production process. Correct, detailed, and complete modeling of constraints is a must for successful planning. This capability is far removed from the nature of an ERP, which focuses on standard processes.
With metals, planning and scheduling are often a compromise where the actions a planner takes will depend on the situation and priorities at hand. Sometimes, a few of the rules and standards can (and should) be stretched. The planner therefore needs a flexible tool that offers clear insights into the different options. It should be easy to test alternatives before finalizing a plan. ERP systems, focused on standard processes, simply cannot be expected to provide this support.
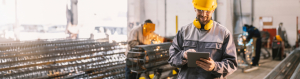
Metal Planning Needs More
While the ERP may have its place, optimized production in metals needs more.
Unlocking optimal value with a 100% fit
Better planning requires detailed insights on all constraints and the identification of potential improvements. While the quality of a plan depends on inputs like demand or capacity, it can also depend on how well various constraints are accounted for. This is especially so in the metals industry, as there are complex installation constraints and planning decisions that have a major impact.
Here, in particular, the materials-driven ERP cannot keep up. It’s unable to account for the many constraints specific to the metals industry, so cannot provide optimal value. Any good planning solution for metals must be able to map out 100% of the specific constraints. It should translate a realistic production scenario into a series of planning restrictions and targets. In unlocking those last few percentage points of value from delivery performance, production cost, or inventory, this 100% fit becomes a differentiator between “average” and “substantially better”. In the metals industry, this famous “last percentage” directly impacts the bottom line.
Scenario-planning and digital twins
In the best-case scenario, the ERP can support some material planning functionalities. However, it’s not really suited to showing the implications of production changes, like when a piece of machinery breaks down or the market changes unexpectedly. It takes time (and probably some additional spreadsheets) to estimate the real impact. The standard ERP is focused on execution. It falls short with scenario planning or providing simulations.
Scenario planning not only ensures better-informed decision-making, it is also an important step in building agility. That agility is needed to evaluate the different options and build predictability into operations. Planners need to see the impact of their decisions before those decisions are made. Then they can optimize resource usage, prevent issues, minimize downtime, and improve production profitability.
Blending the alternatives to future proof the business
ERP cannot future-proof the supply chain, especially as new sustainability factors must now be considered. These factors include fluctuating energy consumption and availability, material recycling, or optimization of routes. Today, finding the best plan, and the most sustainable one means stepping away from fixed production standards, routings, and material requirements. Optimization based on footprint and sustainability parameters is a new and important element. While ERP-based standardization does help with executing plans, it falls short in seeking and combining the best available alternatives.
Ensuring speed and good reaction times
Speed is of the essence in metals planning, alongside rapid reaction times. A response to deviations and disruptions is crucial, and it should be pretty much real-time. For planners, it’s not enough to be able to see the impact of yesterday’s disruptions a day later, especially if counteractions are needed today. ERPs fail when it comes to providing the agility and rapid response times needed to handle unpredictable events. That in turn makes it harder to maintain a competitive edge.
With an increasing number of challenges and unknowns in the external environment, organizations must expect the unexpected. In doing so, they will need a comprehensive, agile planning setup at their disposal. This will help to ensure that the right decisions are made, even if there is little time to make them. Additionally, by mining data that are collected over time, planners can start to spot trends, take a more proactive approach, and avoid issues before they occur.
Platform-Thinking: Combining the Strengths of ERP and APS
Advanced Planning Systems (APS) will empower manufacturers to react in real time and create optimal plans to squeeze out those last few percentage points. It will also create the agility needed for today’s metal supply chain. The strengths of ERP are clear for executing standard processes and managing data, but there’s more to finding the right planning setup. In fact, it’s better to take a step back. Rather than diving into any particular software solution, look at what’s needed and see where it can be found in the market.
From there, visualize a platform that offers the best of what you need. By taking a platform approach, one that merges your ERP and APS, you can get a solution that actually fits your needs, and is not limited by what a single solution can provide.
Both systems have an important role to play in metals, and with legacy planning systems reaching end-of-life throughout the industry, it makes sense to upgrade and rethink the approach. There’s a real opportunity to breathe new life into planning and complement the strengths of both ERP and APS. That’s the route to holistic, effective decision-making.
Find the Right Partner to Guide You
While limitations and opportunities exist in both systems, the design of the overall planning landscape and the interaction between ERP and APS are crucial. The team at Kranz Wolfe Associates & The Logic Factory understands the intricacies of the metals industry and can guide you to find the right APS, one that will work with your ERP.
It’s time to truly engage with real-time planning and to build agility in a changeable environment. That all starts with a good planning process design, which is mapped to the right ERP and APS functionalities.
Help is there, talk to our team. With 20 years of experience behind us, we can implement the right solution, one that can solve the unique puzzle you face with metals planning.