Navigating 2024: Key Supply Chain Challenges in Metals Manufacturing
For metals manufacturers, every new year weaves a tighter knot of complexity. From facing rising inflation to meeting environmental goals due to the climate crisis, they find themselves in a catch-22 asking, “How can I grow my business over time with shrinking profit margins, rising pressure for sustainable practices, and fluctuating prices and demand?”
To make matters worse, IT infrastructure and digitalization in metals production are falling behind other industries, making the navigation of the supply chain even more complex. These may sound like challenging and even desperate times. But you do not need to take desperate measures.
Having supported many leading global organizations in improving their supply chain planning and optimization, we’ve come to understand their fears intimately and want to share them with you. As a bonus, we also offer you our view on how you can sail through these challenging times.
Five upcoming supply chain challenges you should be aware of
1. Sustainability
Metal production has a significant carbon footprint. Despite manufacturers making major efforts to improve recycling rates and reduce emissions, the production of aluminum and steel still contributes more than 10% of CO2 emissions globally. There is also increasing pressure on the industry to earn its “license to operate.”
As the year progresses, the urgency for environmentally-friendly manufacturing will come into sharper focus. Although the shift towards “green metal” started some time ago, it got a big boost last year. During COP28’s Global Stock Take, 200 governments committed to a more renewable future, catalyzing the energy transition from fossil fuels. There is now greater pressure than ever before on manufacturers to produce metals more sustainably (or reduce production).
According to BCG, organizations that lead the way in sustainability could secure long-term competitive advantage. New technologies are on their way but will take time to mature and implement. In the meantime, doing more with less – in terms of energy and resources – is the only viable strategy in the short term. This forms a considerable challenge for supply chain executives. Not only are they forced to squeeze out higher efficiency in their processes, but the question of how to do so remains.
2. Price volatility
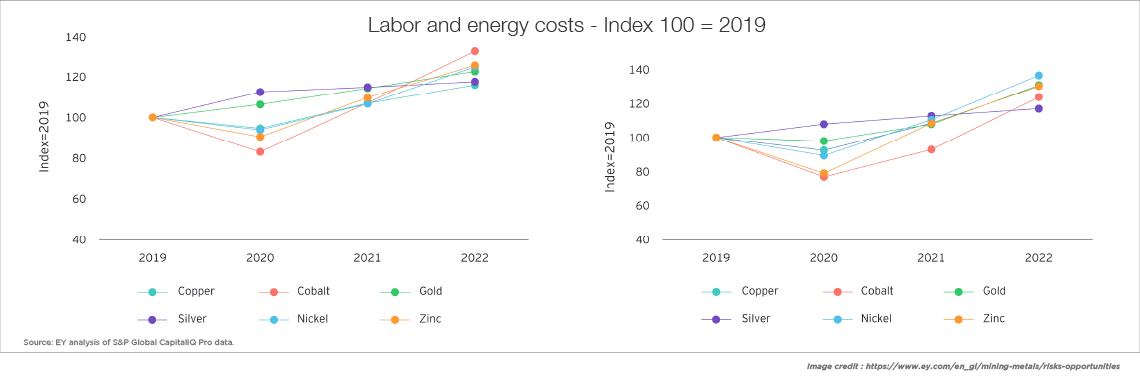
With ongoing global conflicts and the ever-increasing number of disruptions, 2024 will bring heightened price volatility to energy and labor costs. EY has reported that players in metals manufacturing are starting to lose out on their margins. Additionally, the report mentions that reducing carbon footprint through programs and pricing schemes has impacted costs and will only get worse.
Making the right decisions on the pricing of products and the purchase of raw materials and energy has become key to a business’s success (or failure). Great planning requires clean data and timely information on the impact of changes.
The industry appears to lack a comprehensive solution to this problem. We’ve seen many large companies still employing legacy systems, ERPs knitted together with spreadsheets to solve their current issues and come to (delayed) decisions. There are multiple reasons why they are just not enough.
What you do not want is localized siloed planning. Having an end-to-end solution will help with planning against disruptions and subsequent price volatility. Adopting more agile and foresight-oriented planning strategies is needed to mitigate the impact of these fluctuations and secure margins. The directions are clear, but how do you get there?
3. Workforce shortage
“The metal sector is facing an alarming shortage of skilled workers. Demographic change and a lack of young talent have led to a worrying gap between supply and demand.” – Dr. Ing. Stefani Brockmann, Executive Member of the Board of the Steel Institute VDEh. This shortage is particularly acute in organizations urgently requiring digitalization.
There are several reasons why this will continue to happen. The lack of monetary compensation and an aging workforce are major contributing factors. Additionally, adequate training and positioning the industry more attractively in the labor market are equally important.
Widely adopting digital technology like Advanced Planning and Scheduling (APS) solutions will help in attracting the right people with the right skills. With growing interest in AI and increasing digitalization of the supply chain, you might feel the fear of missing out. You want to hop on the ‘right’ train before it leaves the station. But how do you choose the right one?
4. Supply and demand fluctuations
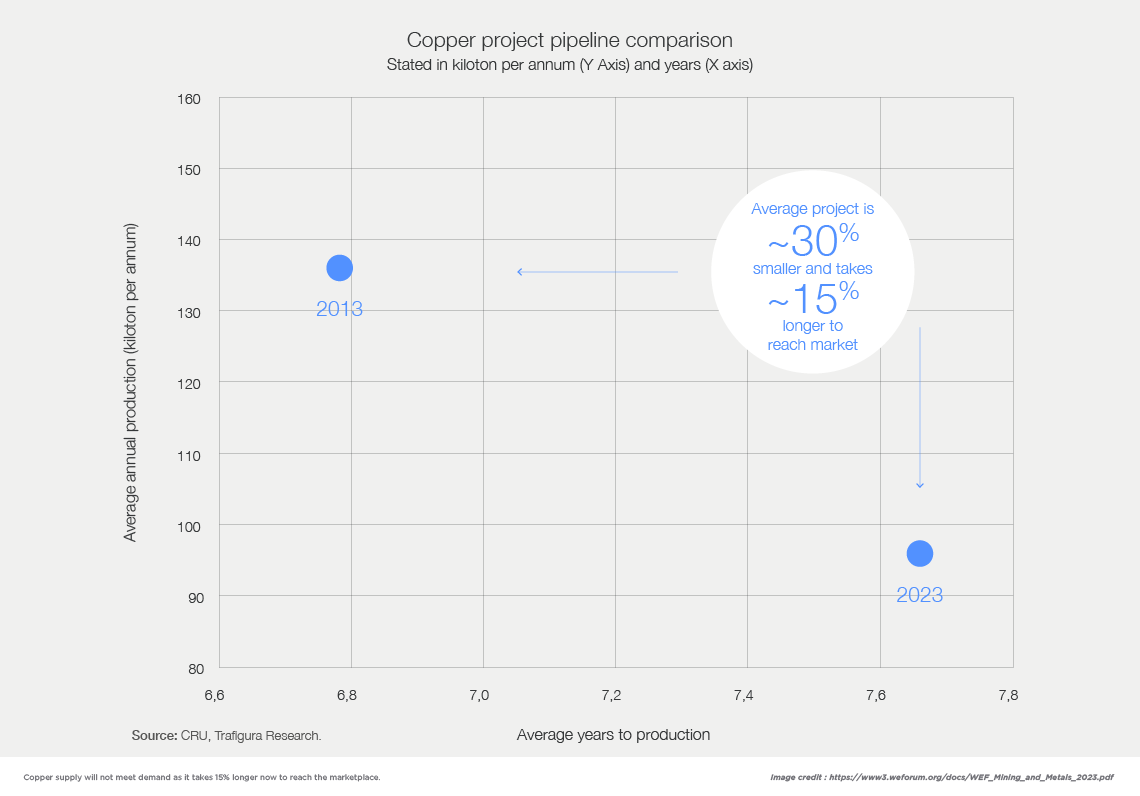
The World Economic Forum (WEF) shares some interesting facts about the supply and demand gap in metals and mining. We’ve already mentioned how the rise in labor and energy costs impacts the industry. They also lead to rapid changes in demand, resulting in fluctuations and difficulties in forecasting demand.
Political instability and global conflicts also cause fluctuations in supply and demand, with customers like car manufacturers lacking crucial supplies. Given the current state of IT infrastructure, it’s hard to see how companies will cope with the increasing pressure to deliver on what’s needed.
The WEF reported that having more efficient and resilient supply chains is critical to avoiding bottlenecks that could slow down or derail the energy transition. We couldn’t agree more. End-to-end transparency, fast reaction times, and scenario planning are key ingredients for an agile supply chain. They are essential for making faster, more informed data-driven decisions. These solutions are not new and could’ve (should’ve) been adopted yesterday. And greenfield solutions might provide results, but they may arrive too late. To achieve desired outcomes, acting now is paramount.
See how The Logic Factory (TLF) helped Glencore, one of the leaders in the metals and mining industry, optimize its operations.
5. Disruptions:
The industry is no stranger to disruptions, but their nature and frequency will evolve. On the one hand, the new energy economy will boost the demand for metals like copper and lithium, creating a temporary shortage. On the other, geopolitical developments threaten to disrupt supply chains on short notice, negatively influencing profitability.
The WEF identifies these challenges but, at the same time, also lists transformation enablers, innovation in technology, and circularity as drivers to reduce the impact of disruptions. However, the transformation cannot be effective without the help of digitalization and Industry 4.0 to boost implementation speed and significantly lower response time on disruptions.
Solutions and digital technology exist, but so far, the adoption rate is much lower in metals than in other industries. Will we witness a rising trend of companies getting into trouble by major disruption that they did not anticipate or could not respond to quickly enough?
There are other elements at play that could make the upcoming year a perfect storm for metals manufacturers. Experts from TLF and Kranz Wolfe Associates (KWA) cover it in more detail in this article.
What you can do about it
The trends and challenges we’ve discussed might sound threatening and even pessimistic. However, the good news is that solutions can be realized through the digitalization of supply chain operations. The power of optimization, simulation, and AI will drive better, faster, and data-driven decisions. In this transformation, manufacturing agility and transparency will play a key role.
Ranging from better resource utilization to meet sustainability goals and over-optimizing margins in a volatile environment to building resilience in your supply chain, the role of true end-to-end digitalization cannot be underestimated. And there are no magic answers or quick fixes.

What we propose is not a revolution but nuanced advice – building on existing data and execution systems. We ask you to adopt an Integrated Hybrid Solution for your metals supply chain planning. An Integrated Hybrid Solution combines the strengths of your ERP and APS. While the former continues to execute standard processes and manage data, the latter can boost your digitalization journey with demand forecasting, scheduling, what-if scenarios, and logistics support.
Both systems have opportunities and limitations, and having the right partner to guide you through the process is crucial. TLF and KWA would support you the whole way – from project planning and implementation to post-implementation support. The time to act is now. Take another important step towards a digital end-to-end supply chain and stay ahead of the challenges.
Interested in discussing how we can help you enhance your supply chain operations in a relatively short time frame? Click the button below for a personalized consultation on how our standard solutions can be configured to fit your business. Do you feel like you get a lot of theory and no help with your current problems? That will change when you speak to us!